TWS Jacksonville is a Great Training Option for Everyone
Learn more about how we can prepare you to advance your career.
Slag – an unwanted byproduct or an essential tool in the welding process?
If you’re at all familiar with welding, you’ve probably come across the term slag before. Despite being a common part of several common welding techniques, there’s still a lot of confusion surrounding it. Let’s clear up that confusion!
What is the meaning of slag in welding?
The American Welding Society defines slag in welding as “a nonmetallic product resulting from the mutual dissolution of flux and nonmetallic impurities in some welding and brazing processes.”
In simpler terms, slag is a solidified layer that’s left on the weld. It’s a byproduct of specific kinds of welding techniques including submerged arc welding (SAW), shielded metal arc welding (SMAW), and flux-cored welding (FCAW)
Have You Considered a Career in the Skilled Trades?
Fill out the form to recieve a no obligation info packet.
Slag is produced as the arc heats up filler metal and the base metals, resulting in a molten weld pool.
Nonmetallic components such as calcium oxides, silicone, and aluminum that can’t form part of the weld are instantly forced out in a series of complex chemical reactions. These impurities harden into welding slag and sit at the top of the weld.
What is the purpose of slag in welding?
Slag might sound like an unwanted side effect of the welding process, but it’s actually crucial to the success of many welding techniques.
When used correctly, slag serves two primary functions:
- It creates a protective layer over a recent weld to prevent it from coming into contact with the air. This reduces the chances of oxidation which can sacrifice the strength of a new weld connection.
- Slag creates an enclosure preventing molten weld pools from moving out of place when welding at awkward angles.
Can you leave slag on a weld?
No, you can’t leave slag on a weld. It plays an important role in the welding process, but slag’s positive effects are short-lived.
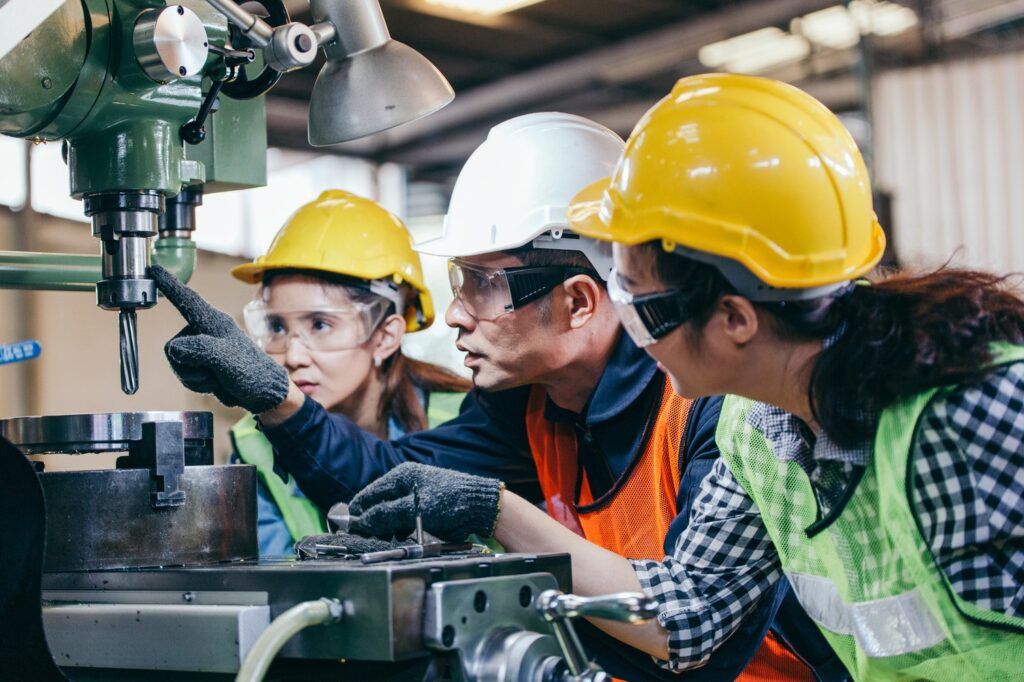
New: Industrial Maintenance
Learn About Our New Advanced Industrial Maintenance Program
Tulsa Welding School is proud to announce our newest program offering available at our Houston & Dallas Metro Campuses – Advanced Industrial Maintenance Technology! Learn the skills you need to take on the industries of manufacturing, distribution, energy production and facility maintenance in as few as 7 months.
When left for too long, slag can contribute to a variety of defects including slag inclusion. That’s why welders must remove the slag before it hardens. Removing hardened slag without damaging the weld is difficult.
What is slag inclusion in welding?”
Slag inclusion occurs when the welding slag gets embedded into the actual weld. The nonmetallic particles that comprise the slag aren’t compatible with the metal components of the weld, resulting in a highly visible defect. Slag inclusions can develop on the surface of the weld or in between different layers.
What causes slag inclusion in welding?
Slag inclusion is a common defect of welding and can result from a wide range of improper welding techniques or accidents. Here are some of the most common culprits:
Mismatched current density
If a welder misjudges the current density required for the welding project, the insufficient struggles to create molten metal, making it harder for the slag to remain on top of the actual weld.
Rapid welding speed
When welders rush through their work or aren’t trained well enough, quick passes can easily result in slag inclusion.
Insufficient removal
As mentioned before, slag needs to be fully removed before a welder can make another pass. When the slag isn’t removed completely or at all, slag inclusion inevitably occurs.
Quick temperature change
If the welding pool is allowed to cool quickly, the slag won’t continue floating on top of the weld.
How do you remove slag from welding?
Once slag has fulfilled its role, welders need to remove it immediately before it hardens and potentially ruins the entire weld.
Some ways of removing welding slag without damaging the work are:
- Chipping
- Flame-cleaning
- Grinding
- Blast cleaning
- Wire brushing
The specific removal method used will be determined by the type of weld being performed.
Interested in learning more about becoming a welder?
Wondering if you have what it takes to become a welder? Read about some of the best personality traits of a successful welder.
This blog has been labeled as archived as it may no longer contain the most up-to-date data. For a list of all current blog posts, please visit our blog homepage at https://www.tws.edu/blog/