TWS is a Great Training Option for Everyone
Learn more about how we can prepare you to advance your career.
To give you insight into companies that recruit TWS graduates, we spoke with Melinda Anderson, Human Resources (HR) Manager with Sabre Industries. Melinda is currently based at their plant in Alvarado, Texas.
Thanks for your time, Melinda. Please give us a brief overview of Sabre Industries.
Sabre manufactures for both the Telecom and Utility industry. When you make a cell phone call, that call pings off cell phone towers, we manufacture those towers. We are also making cell phone towers for the new 5G network they are rolling out. Sabre also manufacture the utility structures that transmit and distribute electricity to your house. In addition to electrical utility & wireless telecommunications, we also galvanize steel products. We have a wide array of services.
Before we continue, please tell us a little about your own career.
Have You Considered a Career in the Skilled Trades?
Fill out the form to recieve a no obligation info packet.
I have a BBA in HR from the University of Oklahoma, and an MBA in HR from Texas A&M Commerce. I’ve been in the HR profession for 15 years, and with Sabre Industries for five and a half years. I’m responsible for three manufacturing plants: Conroe, TX, Alvarado, TX, and York, SC. Sabre bought the Conroe plant in August 2019 with 62 employees; six months later, we are at 163 employees. We are continuing to add capacity to the Conroe Facility. Our focus is hiring welders for all locations right now. We are proponents for internal growth and promotion, and I’ve personally benefitted from that.
So Sabre sounds like a company where people can stay, grow and build a career.
Yes, I truly believe that, wholeheartedly. If you put in the work, they will reward you.
How long has the relationship with TWS been in place, and how did it get started?
We have a longstanding partnership. We go to all the campus job fairs. We’ve hired a lot of grads from Tulsa Welding School over the years. Sabre has locations all over the U.S., and the company has worked with all three campuses. I know the plant in Iowa hires a lot of graduates from the Tulsa campus, and from Jacksonville and Houston. But if you want to work in Texas, Alvarado, (DFW) is hiring too!
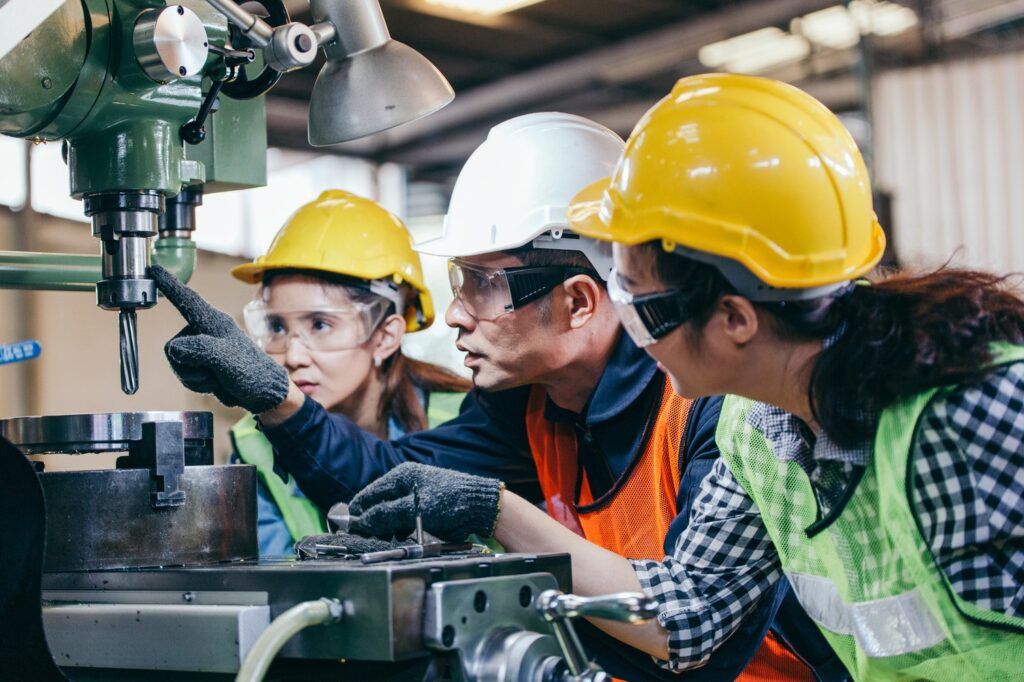
New: Industrial Maintenance
Learn About Our New Advanced Industrial Maintenance Program in Houston
Tulsa Welding School is proud to announce our newest program offering available at our Houston Campus – Advanced Industrial Maintenance Technology! Learn the skills you need to take on the industries of manufacturing, distribution, energy production and facility maintenance in as few as 7 months.
When did you personally first reach out to TWS?
I reached out to Jakis in Career Services in Houston when we made the acquisition in Conroe last summer. Jakis had worked with the recruitment team in Alvarado, so he already knows our folks and the way we work. I’d say about 25% of my current welders are recent TWS grads. Jakis also just sent me a list of his “dream team” top grads. We are calling them now!
Was it the existing relationship that Sabre has with the school that made you reach out?
Yes. Tulsa has always provided very qualified candidates for our locations. The rapport and trust is already in place. I can tell them exactly what we’re building and what our weld test is, and the instructors will help their welders’ practice. So when they come to test, they already know how to do it.
What has impressed you about the school?
I like that TWS is very open to feedback on how it can improve. They want to meet with employers, to find out what we need their graduates to learn. That’s something that I really enjoy. They are always looking to improve, to meet employers’ needs. They are very forward thinking, bending to what the industry requires rather than sticking to a curriculum and simply pushing out graduates.
Could you outline your recruitment process?
Let’s talk about the process here in Conroe, TX. All jobs are posted on our career site and we only take online applications. First step is a phone interview with HR, or an interview at a job fair. Candidates then come to the plant for an on-site interview with the plant superintendent, take a tour, and then take a weld test. We usually decide if we’re going to hire them right then and there, although sometimes we do have to send off their welds for bend tests. But we try to turn it around very quickly. Once they are offered a position, they do a pre-employment drug screen, background and physical, and then orientation is a couple of days. Then they get started!
What kind of qualities do you notice in the TWS graduates who work for you?
They are eager to learn, and they are very excited about growth. I had an applicant who asked me how long the supervisor had been in his role. It surprised me because no one has ever asked me that. I told him it had been 24 years, and asked why he asked. He said he only wanted to work for a supervisor who is an expert at welding because he wanted to continue to learn. I thought that was significant. Sometimes you get graduates who think they know everything. We want graduates that want to learn everything. That guy got a job!
Does the hands-on practice that students get at TWS give them an advantage?
Yes, it does. But I actually think what sets them apart, or gives them an advantage is what I mentioned about the school reaching out to employers. The school finds out how they can tailor their coursework to reflect what is required in the industry. They are trying to teach the students what they need for the production floor, not just “let’s teach this in class”. It’s real-time, real-world training.
Does Sabre have a formal training program?
Safety is hugely important at Sabre, and we spend two full days in safety orientation. In terms of weld training, it depends on the location where they work. We do have some in-house job specific weld schools (not to the extent of Tulsa Welding School), and in-house classes and tests.
All locations have a skill-based pay certification program. It’s a training program and a checklist, so welders know exactly what they need to be able to do in regard to safety, quality, certifications, testing, and job specific training. It is a true training packet that they can use over a three to six-month period. It incorporates at least five people signing off that the employee is certified in that skill set. It helps them advance with career progression, and with pay increases. They don’t sit in a classroom for six weeks. It is on-the-floor training. Most entry-level welders will start tack welding, and they will be paired with a stronger welder so they can learn on the job.
What advice do you have for students to be successful at school, and to have a chance of getting hired at a company like Sabre?
Attendance is a really big deal. It seems that across the U.S., in every industry, we have chronic absenteeism and tardiness issues. Having a willingness to learn and to listen is another really big thing. Sometimes people think they know everything, and they don’t listen. When you graduate from school, you have learned only a portion of what you need to know. Every job is going to be different.
Another thing is patience. When you graduate, have patience. Don’t expect to be immediately paid like a 15-year veteran welder. If you are prepared to go traveling, have the skills to go to the pipeline and get a per diem, then you might make $30 an hour straight out of school, but otherwise you’re not. You need patience and to know your worth. The younger generation has the expectation that they are going to be promoted within the first three months. That’s just not how the real world works. You get the basic skill set in your education, but you have to build on the job experience before advancing.
Any final words of advice?
Have a positive attitude and be safe, no matter what. This is a skilled trade, and welding is unique. Look outside. Everything around you has something that has been welded: your car, that building, that light pole. The need for welders is growing. This is a trade that is in very high demand. There is a lot of potential. Not just career opportunities, but opportunities to make things that change people’s lives. Here’s an example: When Puerto Rico had no electricity because of the hurricane, our Alvarado location built the electrical utility poles, galvanized them, and sent them to Puerto Rico to help restore electricity for those people. Welders do things that effect everyday lives. You just don’t always think about it. If that’s not motivating, I don’t know what is!
This blog has been labeled as archived as it may no longer contain the most up-to-date data. For a list of all current blog posts, please visit our blog homepage at https://www.tws.edu/blog/