TWS is a Great Training Option for Everyone
Learn more about how we can prepare you to advance your career.
Welders often perform their work in awkward and tight spaces, requiring professionals to master a variety of welding positions.
Beyond a practical skill, having the ability to weld in different situations can even increase the income potential of candidates! Out-of-position welding position takes time and practice, making it a crucial technique for welders who want to advance in their careers.
What is out-of-position welding, exactly?
Out-of-position welding is a term used to describe all welding positions other than the preferred flat welding technique.
For example, overhead, vertical, and horizontal welding positions are common examples of out-of-position welding strategies. The complex nature of many welding projects makes it impossible for welders to stay in the flat position.
Have You Considered a Career in the Skilled Trades?
Fill out the form to recieve a no obligation info packet.
It’s not uncommon for welders to work with oversized or immovable objects that require more uncomfortable angles. Skilled tradespeople are expected to learn out-of-position welding techniques even in entry-level positions. It’s an especially common practice in the construction, offshore, and shipbuilding sectors
Why is out-of-position welding hard?
Out-of-position welds are more complex than flat welds. These welding positions require more resources, time, and energy to achieve the same weld quality when compared to their standard counterparts.
Welders have to fight against gravity to keep the weld pool from dripping, significantly increasing the challenge and risk of the project.
Tips for out-of-position welding.
Reconsider the positioning.
A flat weld isn’t considered the standard welding position because of its simplicity.
It’s the ideal welding setup since it’s the easiest to manage. As a result, welders should always avoid out-of-position welding if possible.
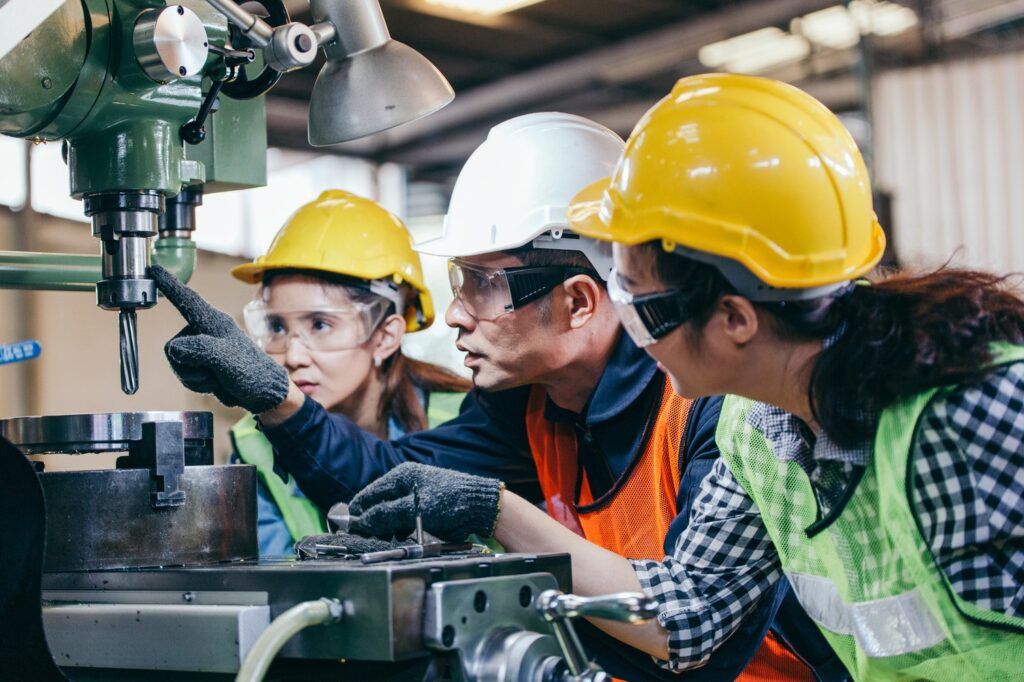
New: Industrial Maintenance
Learn About Our New Advanced Industrial Maintenance Program in Houston
Tulsa Welding School is proud to announce our newest program offering available at our Houston Campus – Advanced Industrial Maintenance Technology! Learn the skills you need to take on the industries of manufacturing, distribution, energy production and facility maintenance in as few as 7 months.
Before striking an arc, take a second to consider the angle. Is it possible to reposition the part so you can weld flat instead of overhead, horizontal, or vertical?
Sometimes a simple 90 or 180-degree transition can save you from unnecessary work and resources. Your first hunch is probably correct, but it’s certainly worth double-checking for those few times if a flat weld really is possible.
Don’t forget the basics.
When confronted with challenging and complex welding projects, it can sometimes be hard to remember the welding basics you learned in trade school.
Although some crucial differences exist, standard and out-of-position welding techniques share critical similarities.
Welders still need to follow the fundamental rules of the trade, such as maintaining a clean work environment, preheating correctly, using enough shielding gas, positioning the joints carefully, and choosing the right current. Keeping these basics in mind when performing an out-of-position weld can make the more complicated parts a little easier.
Adjust the parameters.
A common error welders make when performing out-of-position welds is forgetting to adjust their parameters from in-position welds. This is especially common when moving back and forth between various welding positions in a single project.
Welders have to make necessary adjustments to compensate for the variability brought about by the additional obstacles of out-of-position welding. The essential changes will depend on what kind of welding position you’re performing along with a host of other factors.
However, it’s still important to remember to match the welding parameters with the job requirements.
Practice, practice, practice.
Standard welding techniques require a highly specialized set of skills and expert knowledge to master. Out-of-positions welds, considering their difficulty, require even greater mastery.
The best way to improve these welding skills is to practice, practice, and practice some more. Ideally, you could find a holistic welding program that covers out-of-position welding techniques so you can enter the field with some practical knowledge in this area.
Regardless, the trick is to get as many repetitions with this type of welding as possible to improve your abilities.
Utilize pulsing technology.
Some advanced welding equipment has pulsing abilities, which are great for welders when tackling out-of-position tasks.
As the name suggests, this welding technology switches back and forth between low and high output several times each second, resulting in a pulsing effect. The lower amperage is designed to allow welding puddles to rapidly solidify while the high amperage is intended to make it easier to penetrate.
This pulsing amperage is beneficial when a project requires a spray transfer, since it helps welders stay protected from molten material.
Interested in learning more about various welding skills and techniques? Contact us to learn more about our Professional Welding Training, or read about the different types of welding to further increase your knowledge.
This blog has been labeled as archived as it may no longer contain the most up-to-date data. For a list of all current blog posts, please visit our blog homepage at https://www.tws.edu/blog/